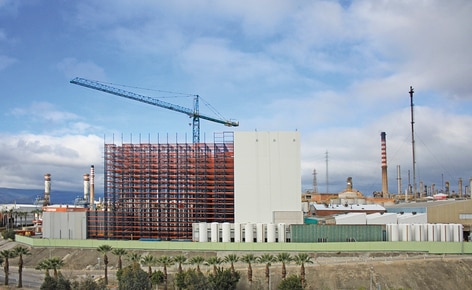
Depósito autoportante automático, optimiza la logística de lubricantes de Cepsa
Cepsa: un caso de éxito en la integración de procesos logísticos
La compañía energética Cepsa confió en Mecalux la construcción para su fábrica de lubricantes de un depósito automático llave en mano de 37 metros de altura en la población de San Roque (Cádiz). En el suministro también se ha incluido el sistema de gestión de depósitos de Mecalux Easy WMS, encargado de gestionar todas las actividades propias del centro.
Quién es Cepsa
Cepsa es un grupo energético, 100% IPIC, que emplea a más de 10.000 profesionales ejerciendo su actividad en todas las fases de la cadena de valor de los hidrocarburos: exploración y producción de petróleo y gas, refino, transporte y comercialización de los derivados petrolíferos y del gas natural, biocarburantes, cogeneración y comercialización de energía eléctrica.
La Compañía ha desarrollado un área petroquímica importante, en alta integración con la de refino de petróleo, en la que fabrica y comercializa materia prima para la elaboración de productos de alto valor añadido que son utilizados, principalmente, para la producción de plásticos de nueva generación y detergentes biodegradables. Cuenta con una notable presencia en España y, a través de una progresiva internacionalización, también desarrolla sus actividades en varios continentes, comercializando sus productos en todo el mundo.
Necesidades de Cepsa
La compañía tenía unos elevados costes logísticos porque, a diferencia del depósito de materia prima, su depósito de productos terminados estaba alejado de la planta de producción.
Ante esa situación, Cepsa se puso en contacto con Mecalux con el objetivo de construir un nuevo depósito automático con la máxima capacidad posible en el lugar que ocupaba el depósito convencional y los talleres de mantenimiento. Además, era indispensable disponer de puestos de picking que le permitiera agilizar la preparación de los pedidos.
La automatización debía iniciarse en la salida de cada línea de producción para que los operarios se limitaran a realizar únicamente las operaciones que demandaran una intervención manual.
Era necesario contemplar los diferentes modelos y medidas de los pallets, así como poder almacenar directamente en las estanterías los “europallets” de: 800 x 1.200 mm, 1.000 x 1.200 mm, 1.150 x 1.200 mm y 1.200 x 1.200 mm.
Al mismo tiempo, se tuvo en cuenta la llegada y su posterior almacenaje, principalmente del exterior, de pallets de medidas diferentes a las indicadas. Una parte de esos pallets contienen productos indispensables para producción, por lo que desde el depósito también se debía proveer su entrega en esta zona.
Otro requisito de Cepsa era que todas las fases de desarrollo y construcción del depósito, incluyendo el suministro del software necesario para gestionar correctamente todas las operativas internas, fuera llevado a cabo por una única empresa. En definitiva, que ejecutara de principio a fin una obra llave en mano bajo la necesidad de construir sin dejar de fabricar el producto.
Características de un depósito llave en mano
El concepto de depósito llave en mano para Cepsa incluía las siguientes premisas:
- Desarrollo, elaboración y legalización del proyecto, contemplando todas las partes que componen el depósito y teniendo en cuenta las distintas normativas aplicables.
- Derribo de las instalaciones existentes donde se ubicaría el depósito, así como su acondicionamiento posterior.
- Preparación del terreno base y la construcción tanto de la losa de hormigón como de los muros perimetrales. Todo ello, con la resistencia y la planimetría idónea para este tipo de depósitos.
- Suministro y montaje de las estanterías, así como de las estructuras necesarias para la construcción del depósito autoportante.
- Suministro, montaje y puesta en marcha de los equipos de manutención: transelevadores (robots de almacenamiento), transportadores, puestos de control, dispositivos para facilitar el picking y todos los elementos auxiliares necesarios.
- Abastecimiento y montaje de los paneles de cerramiento del depósito, tanto de la fachada como de cubierta.
- Construcción de un edificio anexo, donde se encuentran las zonas de recepción de la mercadería procedente del exterior, salidas del depósito, expediciones y picking.
- Suministro y montaje del sistema contraincendios dentro del depósito y en zonas anexas, teniendo en cuenta las normativas existentes. En este caso, Cepsa ya disponía en la planta tanto del depósito de agua como de los equipos de bombeo necesarios.
- Instalar puertas de sectorización entre el depósito y los edificios anexos que funcionen automáticamente en caso de un conato de incendio.
- Instalación eléctrica.
- Sistema de gestión de depósitos. Este sistema debe estar conectado al ERP o sistema informático principal de Cepsa para intercambiar órdenes e información.
Un depósito autoportante como solución
Desde un inicio, Mecalux colaboró estrechamente con los responsables de las diferentes ingenierías de construcción y dirección de logística de Cepsa para determinar qué solución era la que mejor se ajustaba a las necesidades de la compañía.
Después de analizar detalladamente todas las especificaciones facilitadas, Mecalux propuso construir un depósito automático autoportante de 37 m de altura con capacidad para más de 28.000 pallets en una superficie de tan sólo 4.150 m2.
Al disponer de una superficie limitada, se planteó realizar las entradas que van directamente al depósito desde las salidas de las líneas de producción, y las expediciones en el lado opuesto. Separar la zona de entradas y salidas no es una práctica muy habitual, pero en el caso de Cepsa resultó ser la mejor solución.
En un depósito autoportante, las estanterías son parte fundamental de la estructura del edificio y sobre ellas se colocan los cerramientos. Además de su propio peso, deben soportar el de los pallets almacenados, la fuerza del viento, los elementos de manutención (robots de almacenaje), el sismo en base al coeficiente indicado en el lugar de construcción y el peso de nieve que corresponde por normativa.
Los tubos del sistema contra incendios se instalan y se fijan en las propias estanterías, quedando protegidos de posibles impactos ocasionales y ofreciendo un correcto rociado de los pallets.
Para que todas las operativas funcionen correctamente, se instaló el sistema de gestión de depósitos Easy WMS de Mecalux, encargado de gestionar y controlar todas las operativas del centro logístico.
Interior del depósito
Lo forman siete pasillos con estanterías de doble profundidad colocadas en ambos lados; por cada pasillo circula un transelevador del tipo bicolumna con horquillas telescópicas de doble profundidad de prácticamente 34 m de altura.
En longitud, se dispone de 19 módulos de estanterías con 18 niveles en altura de carga que admiten, dependiendo del modelo y medidas, dos o tres pallets cada uno.
Se ha acondicionado una ubicación extra en cada nivel a partir del tercero y hasta el nivel 18 que coincide con los puntos de depósito y de extracción de los transportadores colocados en los extremos de cada calle.
Cabecera de producción
Por este lado se efectúan las entradas de los productos terminados, aunque también dispone de salidas para el producto complementario requerido en producción.
Desde las mismas salidas de las líneas de producción, y una vez la mercadería ha sido palletizada, el sistema instalado por Mecalux ya se hace cargo de los pallets para su depósito y el posterior envío al área de expedición y picking.
Además de la zona de producción que coincide justo con la parte posterior del depósito, hay un espacio reservado para el envasado de contenedores tipo IBC (específico para almacenaje y transporte de líquidos). Esta zona también está conectada con el depósito a través de una segunda lanzadera y de la propia cabecera de producción.
Cabecera de expediciones
Se han dispuesto transportadores de salidas directas hacia los muelles de carga (cinco mediante cadenas y tres mediante rodillos), permitiendo posicionar los pallets por el lado más apropiado.
Por este lado se realiza la entrada de la mercadería procedente del exterior. Para ello, se han instalado los transportadores y los elementos necesarios, incluyendo la posibilidad de remontar pallets de medidas y calidades no apropiadas sobre otros en buen estado.
Además, en esta zona se encuentran los puestos de picking con los equipos de manipulación apropiados y un espacio libre para instalar dos puestos más si las necesidades lo requieren.
También se ha dispuesto una lanzadera que hace de enlace entre las distintas posiciones actuales y futuras. Un circuito de transportadores comunica el depósito con los transportadores de salidas y entradas de las diferentes zonas que componen esta cabecera.
Área de picking
Se sitúa entre los transportadores de cabecera y el conjunto de elementos que conforman la estación de entrada desde los muelles. Hay dos puestos de picking y cada uno de ellos dispone de:
- Circuito en forma de “U” adosado a los transportadores de cabecera y con capacidad para tres pallets origen (dos de ellos en espera).
- Plataforma de trabajo con acceso a los cuatro lados del pallet que está en la posición central. Es ahí donde se realiza la operación de picking propiamente dicha, facilitando el acceso al producto.
- Tres posiciones de pallets destino para poder preparar tres pedidos a la vez. Su ubicación está al lado contrario de la plataforma de trabajo.
- Un manipulador de cajas mediante ventosas colgado de la estructura superior, capaz de moverse en los tres ejes y evitar así la manipulación manual, principalmente de las cajas más pesadas.
- Un terminal informático y dos impresoras.
Además, esta área tiene una zona libre prevista para duplicar los puestos de picking.
Los pallets con pedidos preparados se introducen, utilizando la lanzadera, en la estación de entradas de pallets procedentes del exterior. Estos pallets son flejados en un proceso automático antes de ir a las posiciones de espera dentro del depósito, o directamente al canal de salidas asignado. En ambos casos se desplazan a través de los transportadores de cabecera.
Sistema de gestión Easy WMS: el cerebro de la instalación
Easy WMS controla todos los procesos de entrada, la ubicación del depósito, el stock, las reglas de ubicación, el almacenaje y extracción, los pallets que han de ir a los puestos de picking, el propio picking, los retornos al depósito, etc.
Galileo, el software de control de Mecalux, realiza los movimientos de los distintos dispositivos y máquinas. Además, controla el estado de los elementos que componen todos los circuitos de transportadores, de los propios transelevadores, de sus seguridades internas y externas y el de otros elementos que interactúan con ellos.
Como aspecto destacado, se ha desarrollado un alto nivel de integración entre los sistemas IT del nuevo depósito y el de Cepsa. Este último cuenta con las aplicaciones ERP (SAP) y MES (SEP-PAP) que gestionan integralmente la compra de materias primas, fabricación, control de inventarios y procesos comerciales. Easy WMS recibe automáticamente, mediante interfaces específicas, la información de los productos que se están fabricando, las necesidades de materias primas para la fabricación, la recepción de pedidos de proveedores o los pedidos de clientes.
Este alto grado de integración permite minimizar los errores y facilitar que las operaciones se realicen de forma automática.
Finalmente, un sistema de lector de código de barras permite verificar en el momento de la expedición que los productos que se están cargando son los pedidos por el cliente.
Beneficios para Cepsa
- Alta capacidad de almacenaje en un espacio reducido: el depósito autoportante permite ubicar 28.630 pallets en una superficie de 4.150 m2.
- Ahorro de costes: la automatización del depósito autoportante y la conexión directa con las líneas de producción le han permitido a Cepsa ganar eficiencia a la vez que reducen costes de personal y logísticos.
- Control total: gracias al SGA de Mecalux Easy WMS, Cepsa controla todos los procesos y operativas que se producen dentro del depósito.
Depósito automático autoportante en Cádiz (España) | |
---|---|
Capacidad de almacenaje: | 28.630 pallets |
Peso máximo del pallet: | 1.000 kg |
Altura del depósito: | 37 m |
Nº de transelevadores: | 7 |
Tipo de transelevador: | bicolumna |
Tipo de horquilla: | doble profundidad |
Nº de lanzaderas: | 3 |
Sistema constructivo: | autoportante |
Galería
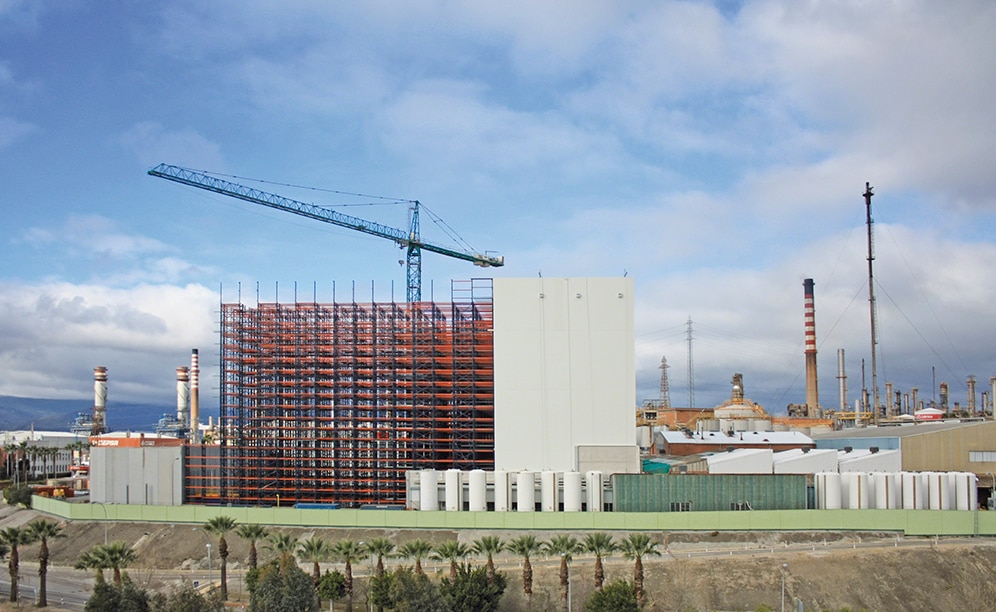
Consulte con un experto